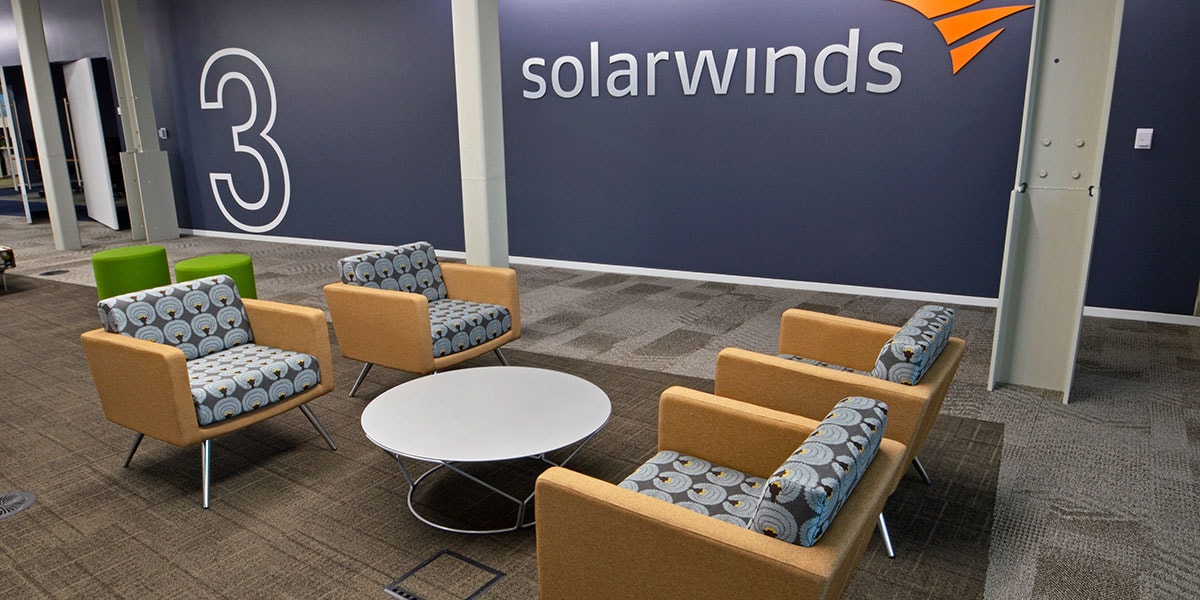
Ensuring Healthy Workplaces
How Flooring Can Impact Indoor Air Quality
By Bill Imhoff, President & Chief Executive Officer at Intertech Flooring / W.E. Imhoff Inc.
Businesses and employees want to get back to work. As in, get back to the workplace. But a safe return to public workspaces will require attention to many facets of the working environment. Among them is the critical importance of ensuring indoor air quality.
That point was made clear in the Centers for Disease Control and Prevention’s recommendations in July to businesses as they prepare to reopen. Before resuming business operations, the CDC noted several key readiness tests: improve ventilation, increase airflow to occupied spaces, and increase air filtration.
Why the Concern over Indoor Air Quality?
Now more than ever, our awareness is heightened over what’s in the air we breathe. We know that outdoor air contaminants can impact our health. Just ask any Central Texan who suffers from Cedar Fever each winter. We face allergens and pollutants outdoors. But move indoors and the risk of exposure to air contaminants can jump two, five or even 100 times higher than outdoor levels, according to EPA studies. In fact, “The EPA and its Science Advisory Board consistently rank indoor air pollution among the top five environmental health risks to the public,” notes a recent UConn Health study on occupational health environment.
Flooring Can Impact Air Quality
While it might not be the first thing that comes to mind in improving your building’s air quality, flooring plays a surprisingly important role in creating a healthy building environment. Aesthetics, comfort and noise abatement traditionally have been the key factors in choosing a commercial building’s flooring products. But in today’s uber-cautious and health-focused environment, building owners and managers are wise to put “improves air quality” among the top of a flooring product’s selection criteria.
Among the things to watch for are:
Volatile Organic Compounds.
Some flooring products and installation techniques produce harmful volatile organic compounds (VOCs). VOCs are gases emitted from certain solids and liquids that can have short- and long-term impacts on health. While many carpet manufacturers have adapted to offer no-VOC carpeting, some carpets and glues still emit VOCs. An environmental or flooring consultant can conduct a carpet odor test to be sure your carpeting is not one of them.
Formaldehyde.
Some studies have found a correlation between some laminate flooring and the presence of formaldehyde, which can impact indoor air quality and the health of your employees. But there’s not a one-size-fits-all answer.
Consumer Reports found wide variations among the products it tested: “The prefinished solid-wood flooring we tested had consistently lower formaldehyde emissions—near or lower than what we think it should be—than the engineered wood and laminate. It’s likely that the glues and resins those products are made with emit formaldehyde. That said, formaldehyde levels varied widely among products and even within samples from the same engineered-wood or laminate plank.”
The best advice: if you are considering laminate flooring, ask an expert to conduct an emissions test.
Mold.
Any building, old or new, can be susceptible to mold. The key to fending off mold in yours is to keep moisture at bay. Carpet is a prime candidate for mold, and hence should be carefully considered before installing in office spaces where spills or water access could be likely. Wet carpet can breed mold in less than 48 hours if left unaddressed.
Not all moisture issues are the result of a plumbing mishap or repeated coffee spills. A poorly installed floor surface can be the cause of moisture problems, too. Pre-installation testing and concrete moisture mitigation can save your company thousands of dollars in flooring problems. You want to start any flooring installation with a clean concrete surface, free of form release agents, curing compounds, surface hardeners, oils, grease, food, chemicals, or other contaminants. Previously applied coatings or toppings may need to be removed. Dust, including new dust generated by surface shot blasting or scarifying, must be removed, too.
If undersurface moisture is detected, mitigating it quickly and correctly is important. A mitigation system is designed to mitigate moisture emission issues including pH, moisture vapor, and air movement through the slab so that any and all finish surfaces may be applied to ensure long-lasting use and acceptable air quality.
Asbestos.
In the 1950s, vinyl sheet flooring and floor tile manufacturers began using asbestos to improve insulation and damage resistance. The use of asbestos in new vinyl materials has been largely phased out as research uncovered serious health concerns. Many buildings constructed before 1980 still contain old asbestos vinyl flooring, however. Left undisturbed, asbestos-containing floors will not release fibers into the air. But, damage and deterioration can make the release of fibers more likely, and create unsafe air quality.
Underfloor Air Improves Quality, Efficiency
Underfloor air distribution systems with raised access flooring have become popular choices for building owners and managers seeking both air quality and efficient energy use. These underfloor systems deliver air through diffusers in the floor, with the intent of maintaining comfort and indoor air quality levels only in the occupied lower portion of space.
The floor surface is raised as low as 7 to 12 inches to accommodate the underfloor system, and can be finished with a variety of green-friendly materials. For office environments, panels can be covered in glue-less carpet tiles with zero VOCs, conductive and static-dissipative vinyl, wood, or high-pressure laminate.
Among their many benefits (greater comfort, reduced energy use and significantly lower building costs), underfloor air distribution systems also are a win for indoor air quality, according to the Center for the Built Environment at the University of California, Berkeley. “Improvement in indoor air quality can be achieved by delivering the fresh supply air near the occupant at floor or desktop level, allowing an overall floor-to-ceiling airflow pattern to more efficiently remove contaminants from the occupied zone of the space,” it notes.
Summary
As businesses and employees anticipate a return to commercial workplaces, indoor air quality will be critical to creating a healthy building environment. Making wise flooring choices can help mitigate airborne contaminants and ensure a safe workplace.
Bill Imhoff is President/CEO of Intertech Flooring, leads three regional offices serving commercial clients across Texas and the Southwest.
This article was originally published in the Austin Business Journal August 13, 2020, and is used with permission The original blog can be accessed here. As an invited member of the Business Journal’s Leadership Trust, Bill provides thought-leadership content and advice to the Austin business community around his areas of expertise, including commercial flooring, entrepreneurship, leadership and workforce development.
Recent Posts
Need Samples?
Order from multiple vendors, all at once!
You’ve Got Better Things To Do...
Enjoy our one-stop approach to easy sample orders.