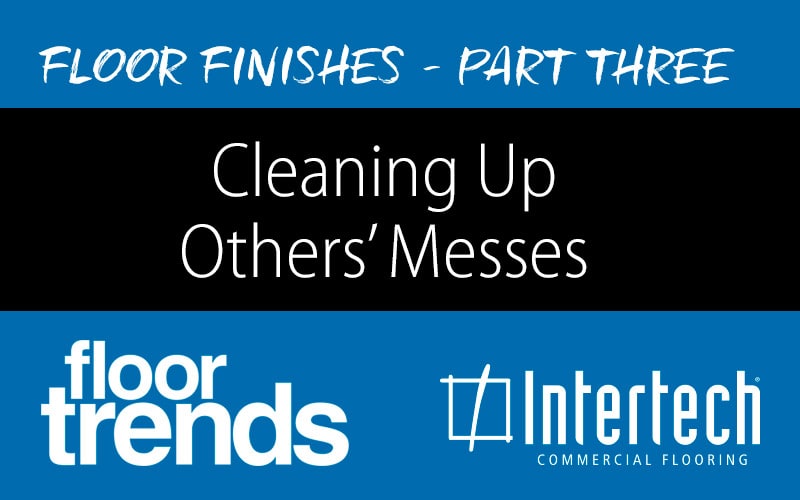
Cleaning Up Others’ Messes – Part Three
Our concrete specialists are often called upon to fix others’ mistakes in dealing with moisture issues. And while there have been a few instances where we declined the request – recognized alkali–silica reaction (ASR) and suspected concrete contamination, to name a couple – we actually thrive on the challenge of resolving difficult problems. When it comes to these situations, we know that there are no partial fixes with moisture. You either fix the floor permanently or you do not. You get one crack at it and you had better know what you are doing.
Often, a change of tenant and new finishes required in a renovation exposes attempted fixes under old stressed flooring, indicating a lack of due diligence or a history of a previous attempt at a now failed ‘band-aid’ on the slab.
The most difficult moisture-related problems we’ve dealt with are those with alkali–aggregate reaction (AAR) conditions. This is an active, dynamic cracking of concrete in the range of five to six years old or older that cannot be corrected with negative side barriers because the sealer will be compromised by future cracking. There are only very subtle attributes that give a clue to the problem, yet any slab with moisture problems over six years old must be suspect in the diagnosis phase.
Any moisture or pH problem can be fixed, but it comes at a price. One Austin high-tech facility came to us after grappling with moisture problems for more than a decade. The fix at that facility involved removing the flooring and preparing, sealing and cementing the original concrete. The approach encapsulated the high humidity in that floor. The facility invested hundreds of thousands of dollars to fix the problem, but it was critical that the flooring be able to bear the weight of large, heavy equipment without buckling.
Another installation required a jackhammer to get to the bare slab and sanding to expose a clean, bare concrete surface. A barrier to seal off the moisture that had soaked into the slab was applied, which, in turn, was covered by a heat-welded, self-coving sheet vinyl. This repair involved many thousands of dollars in testing to arrive at the ultimate solution.
In every case, fixing a floor problem means delays, downtime and cost. Selecting a flooring contractor with extensive product knowledge, field experience and good business ethics is critical in today’s market of tight margins and short timelines.
When it comes to concrete moisture, there’s no substitution for partnering with a trusted and proven concrete expert whose standard is doing it right the first time.
Ask virtually any commercial general contractor to name some of the most costly and problematic challenges in their work, and you are likely to hear a common answer: moisture-related floorcovering issues. This is the third part in a three-part blog series on best practices in concrete moisture mitigation by Intertech’s concrete experts.
Read the whole series on Floor Finishes:
- Part 1 – Floor Finishes – Doing things right the first time
- Part 2 – Floor Finishes – The one step you don’t want to skip
- Part 3 – Floor Finishes – Cleaning up others’ messes
Recent Posts
Need Samples?
Order from multiple vendors, all at once!
You’ve Got Better Things To Do...
Enjoy our one-stop approach to easy sample orders.