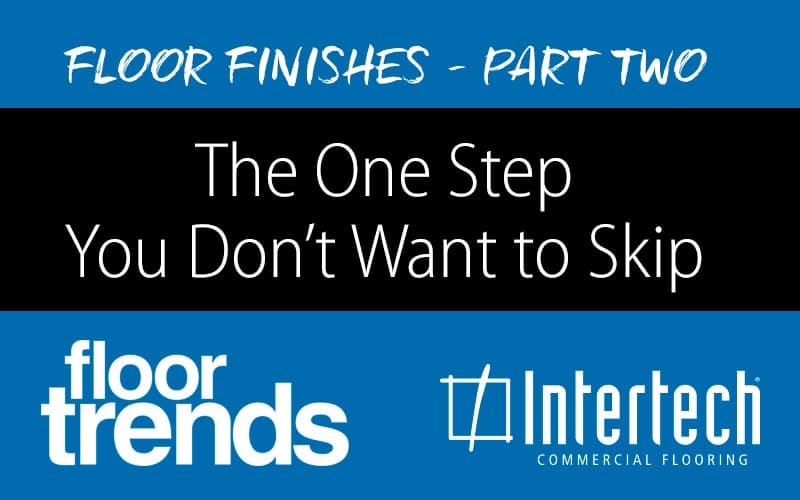
The One Step You Don’t Want to Skip – Part Two
When the Intertech concrete solutions team is called to assess flooring failure due to moisture, we often find it occurred following either poorly run testing – or worse yet, no testing at all – prior to installation. The fact is, in today’s high-cost, low-margin construction economy, it simply is not enough that flooring contractors are knowledgeable in product makeup, green flooring, the evolution of adhesives, construction scheduling, and efficient project management. Without carefully choosing a flooring contractor that knows about pre-installation and concrete moisture mitigation techniques, the general contractor and building owner can easily find themselves dealing with costly fixes and project delays.
Pre-installation testing is the very essence of the success or demise of a good project. It is critical that the flooring contractor conduct a thorough risk assessment before placing any finish products on the concrete surface. Avoiding preventable problems is just as important as providing a quality installation.
Testing should not be considered as simply another project function; rather, it should be a serious analysis or discovery of a risky or impossible environment in which to place a finish. It is only when the floor finish becomes threatened or fails outright that the testing history of the floor comes under much greater scrutiny.
What can you do to ensure your flooring is adequately tested on the front end? Be sure your flooring contractor can plainly discuss the testing procedure, and why it makes sense for your situation. It’s unlikely a contractor can ‘fake’ knowledge about the testing he or she is recommending, and certainly will not be able to ask the necessary questions required without a thorough knowledge of testing and test meaning. Look for a contractor who is ICRI-certified, lending the credibility of a professional who truly understands the nature of what is going on and what has to be examined. If testing is run inaccurately – and even by so-called experts, it often is – the test may produce inaccurate data upon which costly decisions are made that could later result in flooring failure.
If you face a flooring failure, an ICRI-certified expert will first look at the history of the floor: what pre-installation testing was conducted and the results; what type of floor failed and for how long; building topography; as built (vapor retarder) and then alkalinity in a presently stressed or failing condition next. A whole host of other factors must be known as well. What has been tried and failed? Whose warranty did not cover the issue if a solution was applied and failed? Is the ground out of play? What kind of finish will be applied to the corrected floor? How much traffic will it bear?
Doing things right the first time is always preferable to cutting corners only to pay later. That mantra holds true in life, and in commercial construction.
This is the second in a three-part blog series on best practices in concrete moisture mitigation by Intertech’s concrete experts.
Read the whole series on Floor Finishes:
- Part 1 – Floor Finishes – Doing things right the first time
- Part 2 – Floor Finishes – The one step you don’t want to skip
- Part 3 – Floor Finishes – Cleaning up others’ messes
Recent Posts
Need Samples?
Order from multiple vendors, all at once!
You’ve Got Better Things To Do...
Enjoy our one-stop approach to easy sample orders.